The Art of Efficiency: Systemizing and Prioritizing Paintless Dent Repair for Technicians
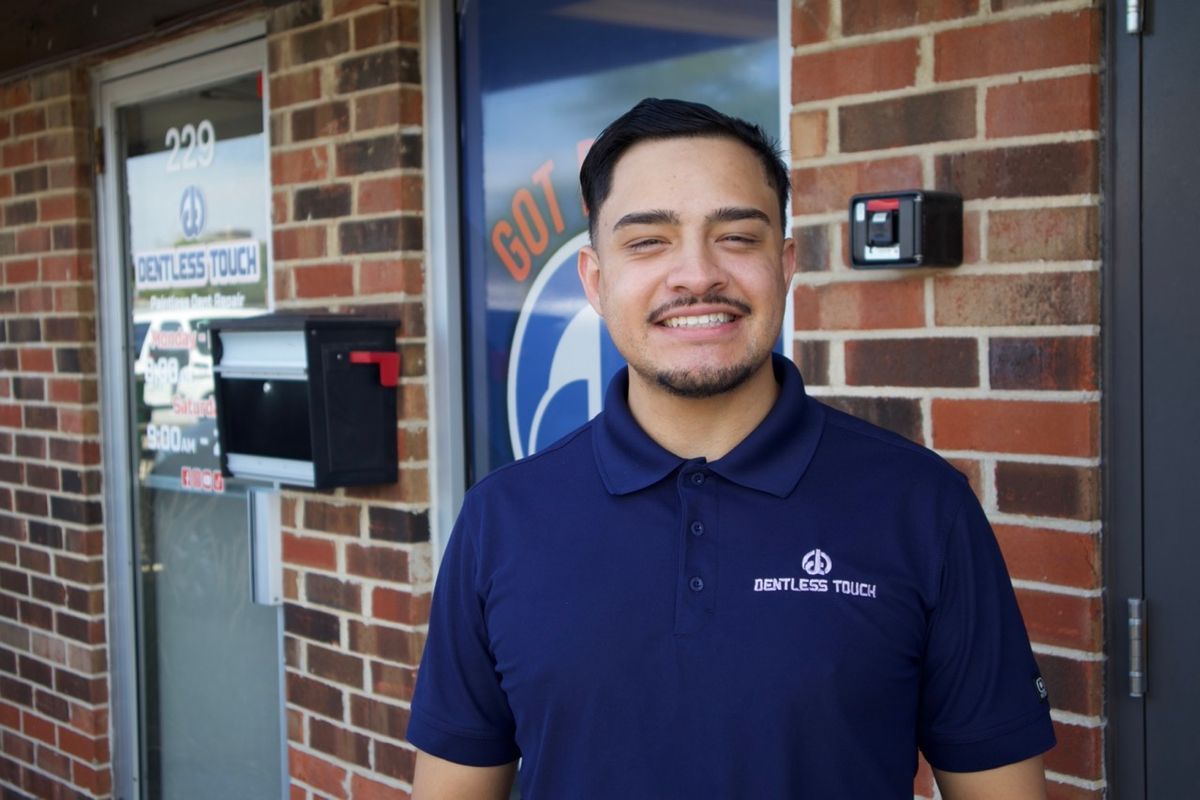
In the world of automotive repair, Paintless Dent Repair (PDR) stands out as a true art form. Skilled technicians adeptly reshape metal surfaces to their original glory without the need for paint or filler. However, beneath the surface of this craft lies a need for systematic processes and prioritization. In this article, we will explore the myriad benefits of systemizing and prioritizing PDR for technicians, along with examples of the systems and processes they can implement.
The Benefits of Systemizing and Prioritizing PDR
- Enhanced Efficiency:
Efficiency is paramount in any industry, and PDR is no exception. Systemizing the repair process ensures that technicians can complete more jobs in less time, ultimately leading to increased profitability. By prioritizing tasks and following a structured workflow, technicians can reduce unnecessary downtime and streamline their operations.
- Consistency in Quality:
Quality is the hallmark of a skilled PDR technician. When you establish systematic procedures, you create a consistent standard of quality that customers can rely on. Each dent repair job should meet the same high standards, which not only pleases customers but also builds a strong reputation for the technician.
- Time Management:
Systemizing PDR allows technicians to manage their time effectively. By following a clear sequence of steps, they can allocate the right amount of time to each task, preventing bottlenecks and ensuring timely completion of jobs. This, in turn, leads to higher customer satisfaction and the potential for more referrals.
Before PDR - During PDR - After PDR
Before PDR |
During PDR |
After PDR |
1. Inspect the vehicle thoroughly to identify all dents and their locations. |
1. Begin the dent repair process by assessing the dent's size, depth, and location. |
1. Perform a final inspection to ensure the repair meets quality standards. |
2. Take clear photographs of each dent for documentation. |
2. Use appropriate PDR tools and techniques to reshape the damaged area. |
2. Clean the repaired area and surrounding surfaces to remove any residue. |
3. Prepare a detailed estimate for the customer, including cost and time frame. |
3. Maintain a clean and organized work area to avoid tool mishaps and maintain safety. |
3. Review the completed repair with the customer, ensuring satisfaction. |
4. Gather and organize the necessary PDR tools and equipment. |
4. Monitor the progress of the repair, making adjustments as needed. |
4. Document the repair process, including any challenges or deviations from the plan. |
5. Review any customer preferences or special requests. (Touch Up Paint, Scratch Removal) |
5. Communicate effectively with the customer, providing updates on the repair's status. |
5. Provide the customer with a final invoice, detailing the services rendered. |
6. Ensure personal safety by wearing appropriate protective gear, such as gloves and eye protection. |
6. Double-check the repaired area for imperfections and make any necessary refinements. |
6. Discuss maintenance and care instructions with the customer to preserve the repair. |
7. Set up a designated workspace with proper lighting |
7. Maintain proper technique and pressure to avoid overworking the area. |
7. Request feedback from the customer to gauge their level of satisfaction. |
8. Prepare any required the vehicle for repair |
8. Continuously assess the repair's progress, ensuring it meets quality standards. |
8. Address any concerns or issues raised by the customer promptly and professionally. |
Examples of Systems and Processes for PDR Technicians
- Inspection and Assessment:
A systematic approach begins with a thorough inspection and assessment of the vehicle. Technicians should create a checklist to identify all dents, their size, and location. Photographs can be taken for documentation. This systematic approach helps in prioritizing repairs and estimating the time required for each.
- Prioritization Matrix:
Not all dents are created equal. To prioritize repairs, technicians can create a matrix that considers factors like dent severity, location, and customer preferences. For instance, a small dent on a highly visible part of the car might be prioritized over a large dent on an inconspicuous area.
- Workflow Standardization:
Develop a standardized workflow for dent repair. This includes processes for accessing and repairing dents, the sequence of tools to use, and safety protocols. Having a step-by-step guide ensures that technicians don't miss crucial steps and maintain consistent quality.
- Tool Organization:
Efficiently organizing tools is vital for a streamlined operation. Designating specific tool locations, labeling, and ensuring proper maintenance will prevent wasted time searching for the right tool during a repair. Dentless Touch uses various carts to keep technicians efficient and organized.
- Documentation:
Maintain detailed records of each repair job. This includes the initial assessment, photographs, work performed, and the final assessment. Documentation helps in tracking progress, ensuring quality control, and resolving any disputes with customers. (Not only does this prepare our technicians for the begining of the repair by having video, but these pieces can be used for overall content creation for Dentless Touch)
- Customer Communication:
Implement a system for effective customer communication. Provide clear estimates, timelines, and regular updates on the progress of repairs. Well-informed customers are more likely to be satisfied and recommend your services to others.
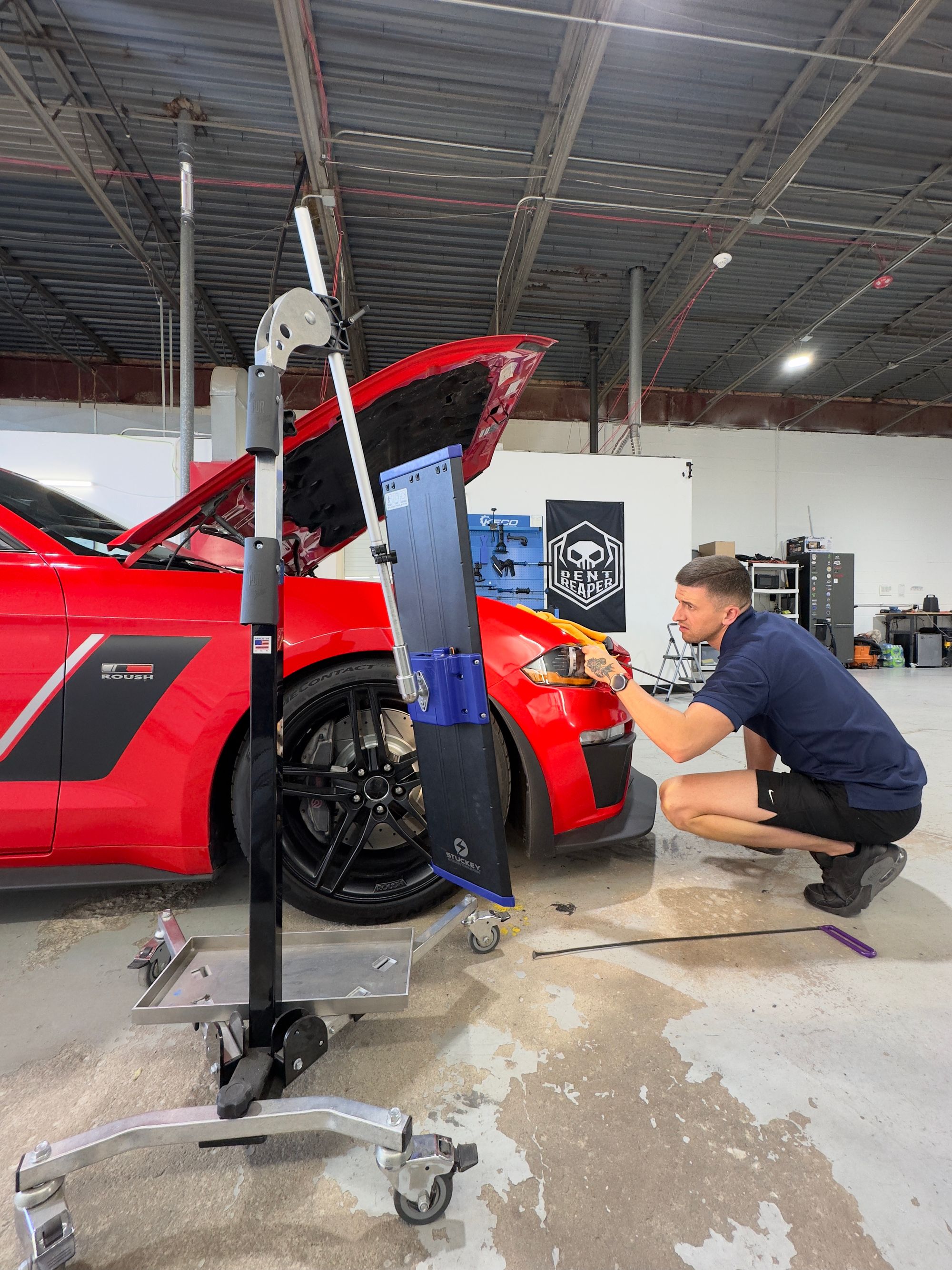
Paintless Dent Repair is not just a skilled trade; it's also a business. To thrive in this field, technicians must embrace systemization and prioritization. By creating standardized processes, technicians can achieve higher efficiency, consistent quality, and better time management. The benefits of such an approach not only benefit the technicians but also lead to increased customer satisfaction and loyalty. In the world of PDR, the art of efficiency is as important as the art of dent repair itself.
Dentless Touch Chicago
229 Eisenhower Lane S.
Lombard, IL 60148
Tel: (847) 366 - 2626
Comments ()